Procédure essai de pression canalisation PE
L’essai du réseau sous pression hydraulique intérieure est la caution finale donnée par l’entrepreneur au maître d’œuvre sur la qualité de sa prestation. Il doit être réalisé dans les conditions prévues au C.C.T.G. (Fascicule 71 relatif aux ouvrages d’adduction d’eau), ainsi qu’aux conditions d’un éventuel cahier des clauses techniques particulières du contrat. La présence du maître d’œuvre ou d’une personne habilitée à signer le procès-verbal est indispensable. Les épreuves consistent en des mises en pression destinées à contrôler l’étanchéité des conduites. Compte-tenu du module d’élasticité et du coefficient de dilatation du Polyéthylène, il est parfois difficile de maintenir dans le temps une pression constante à l’intérieur de la canalisation. A cette fin, le Fascicule 71 comporte une méthode spécifique au Polyéthylène qui est présentée ci-après.
Facteurs à prendre en compte pour la réalisation des essais
Les poches d’air résiduelles se dissolvent dans l’eau de façon réversible pendant l’épreuve, et amènent une chute de pression. Comme dans toute conduite, il faut donc effectuer lentement le remplissage de la conduite, par les points bas du réseau, en ne dépassant pas un débit de l’ordre de 0,1 litre/seconde pour un DN < 90, ou de 0,5 litre/seconde entre DN 90 et 160, ou 2 litres/ seconde à partir de DN 200. Dans ces conditions, il ne se forme que peu de poches d’air, et la purge aux points hauts, indispensable avant toute mise en pression, en est grandement facilitée.
Il convient de réaliser l’épreuve officielle après la pointe diurne de température, et d’éviter les essais nocturnes : en effet, dans le cas d’un tronçon incomplètement remblayé, ou posé en aérien, si la température ambiante s’élève notablement entre le début et la fin des essais, le tube se dilate davantage que l’eau et la pression peut chuter, d’environ 0,5 à 1 bar pour une variation de 10°C. Sous l’effet de la pression intérieure, la canalisation en Polyéthylène « gonfle » légèrement, avec une augmentation de diamètre qui peut atteindre 1,5 à 2 % après quelques heures. Il est donc nécessaire de la mettre en pression préalablement à l’épreuve officielle, pour éviter que ce phénomène normal n’amène à une erreur de jugement. Il est recommandé de ne pas tester des tronçons de longueur supérieure à 500 m en terrain plat. Dans le cas de réseaux présentant une dénivelée importante, il faudra tester le réseau par tronçons déterminés, de façon à ce que la pression au point le plus bas de chaque tronçon ne soit pas supérieure à la PN du composant. Afin que cette procédure d’essai soit représentative, il est nécessaire que la pression de 2ème phase soit au moins de 1 bar au point haut du tronçon.
Généralité
Un réseau ou tronçon de réseau est caractérisé notamment par les trois pressions suivantes :
- DP (Design Pressure) : pression de calcul en régime permanent. Pression maximale de fonctionnement du réseau ou de la zone de pression fixée par le projeteur en tenant compte des développements futurs mais non compris le coup de bélier.
- MDP (Maximum Design Pressure) : pression maximale de calcul du réseau ou de la zone de pression fixée par le prescripteur, y compris le coup de bélier et tenant compte des développements futurs.
- STP (System Test Pressure) : pression d’épreuve du réseau. Pression hydrostatique appliquée à une conduite nouvellement posée de façon à s’assurer de son intégrité et de son étanchéité. C’est à partir de ces pressions que les composants du réseau seront choisis.
Le concepteur du réseau est amené à choisir successivement :
- Le groupe d’application selon le fluide transporté (AEP, Industrie, Eau non Potable, Gaz, etc…).
- La PN des composants En fonction de la pression du fluide convoyé, du détimbrage envisagé et des contraintes éventuelles apportées par l’environnement extérieur ou la pose, le choix de la PN d’un composant s’effectue en tenant compte des niveaux de pression caractéristiques du réseau.
Par conséquent, lors du choix de chacun des composants (tube, mais aussi raccord, bride, et autres accessoires), le concepteur doit vérifier que :
- La DP (pression de calcul en régime permanent) calculée pour le réseau reste inférieure à sa PFA (=PN/(f(t)*f(a)) pour le tube).
- La MDP (pression maximale de calcul, y compris le coup de bélier) envisagée pour le réseau reste inférieure à sa PMA (=2*PN pour le tube).
- La STP (pression d’épreuve du réseau) prévue reste inférieure à sa PEA (=1,5 PN pour le tube).
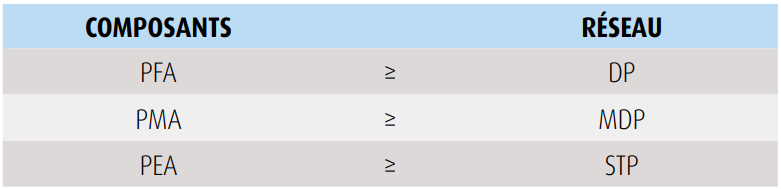
Essais selon le fascicule 71
Le Fascicule 71, édition 2003, prévoit des conditions spécifiques d’essai pour les tubes en PE. Il s’agit d’un essai simple et bref au cours duquel on provoque une contrainte dans le tube en Polyéthylène en le maintenant à la pression d’épreuve pendant 30 minutes. L’ouverture de la vanne de réglage réduit la pression à une valeur spécifiée, puis la vanne est refermée. Une remontée ultérieure de pression dans la conduite démontre l’absence de fuite.
Cet essai simple par « tout ou rien » est représentatif, à condition que le tronçon ait été bien purgé d’air. Les épreuves sont réalisées comme suit :
- Appliquer une pression d’épreuve (STP) (*) égale selon le Fascicule 71 à la pression maximale de calcul (MDP) (*) de la conduite, et au moins égale à 6 bars, et la maintenir 30 minutes en pompant pour l’ajuster.
- Ramener la pression à 3 bars à l’aide de la vanne de purge. Fermer la vanne pour isoler le tronçon à essayer.
- Enregistrer ou noter les valeurs de la pression aux temps suivants :
- entre 0 et 10 minutes : 1 lecture toutes les 2 minutes (5 mesures)
- entre 10 et 30 minutes : 1 lecture toutes les 5 minutes (4 mesures)
- entre 30 et 90 minutes : 1 lecture toutes les 10 minutes (6 mesures)
Les valeurs successivement enregistrées doivent être croissantes puis éventuellement stables, en raison de la réponse visco-élastique du Polyéthylène (voir graphique ci-dessous).
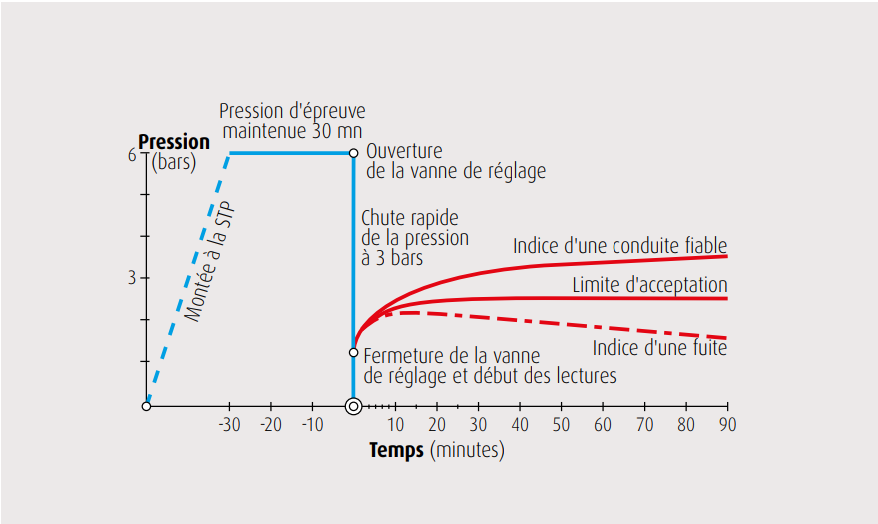
On obtient normalement une bonne indication en 90 minutes. Si durant cette période la pression diminue, c’est le signe d’une fuite sur le tronçon : vérifier en priorité tous les assemblages mécaniques avant d’inspecter les soudures. Toute anomalie constatée doit être rectifiée et l’épreuve recommencée.